Blog
- Home
- Blog
- OEM service
- Differences Between Aluminum and Plastic Reflectors
Differences Between Aluminum and Plastic Reflectors
September 20,2024
Aluminum reflectors are typically made from aluminum alloys such as 1100, 1090, 1070, 1060, or 1050. The choice of alloy depends on the reflector's shape and the required surface treatment. For example, 1050 aluminum alloy is suitable for reflectors or trims that are formed by bending, while 1100 or 1090 alloy is preferred for reflectors requiring anodization and higher surface reflectivity.
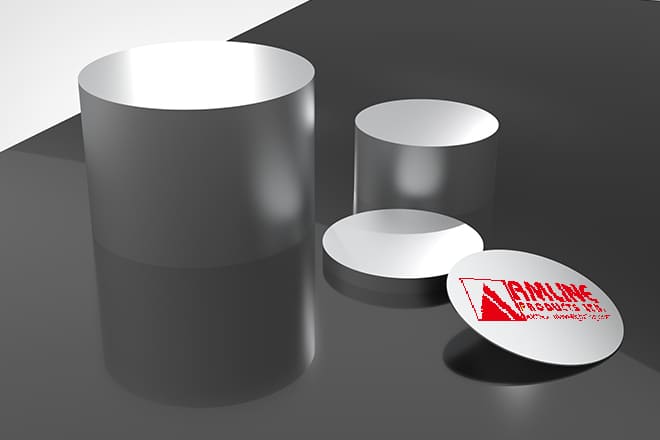
Plastic reflectors, on the other hand, offer a wide variety of material options. Most reflectors on the market are made from these two materials, PC (Polycarbonate) and ABS (Acrylonitrile Butadiene Styrene). Through careful mold polishing or surface coating, plastic reflectors can achieve effective light reflection. However, it's crucial to consider the heat resistance of the plastic used. Even within the PC material category, factors such as the polymer used, manufacturer, and thickness of the finished product can significantly impact flame resistance. When reflectors are placed near unshielded, high-voltage electrical components, selecting a material with UL 5VA flame rating ensures better safety.
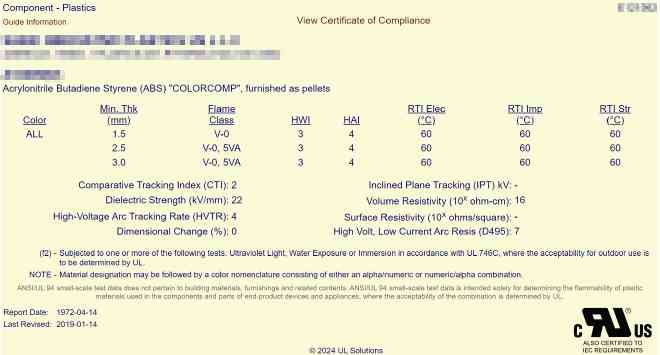
International safety standards such as UL, ETL, or CB place a strong emphasis on the flame resistance of materials used in lighting fixtures. If plastic reflectors are chosen for production, it is essential to ensure that the material meets the required specifications, as additional testing for flame resistance and weatherability is often necessary during certification. By contrast, if aluminum alloys are used for reflectors or trims, these additional tests can often be bypassed.
Still have questions about material selection? Feel free to contact Amline for more detailed consultation. We offer a variety of reflector and trim products made from aluminum or plastic(PC, PMMA, ABS … etc), and other plastic or metal materials.
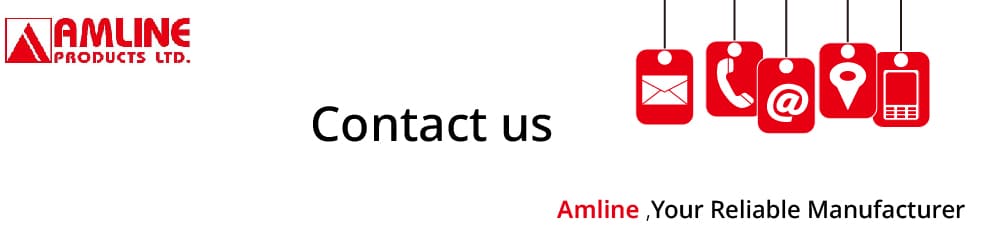
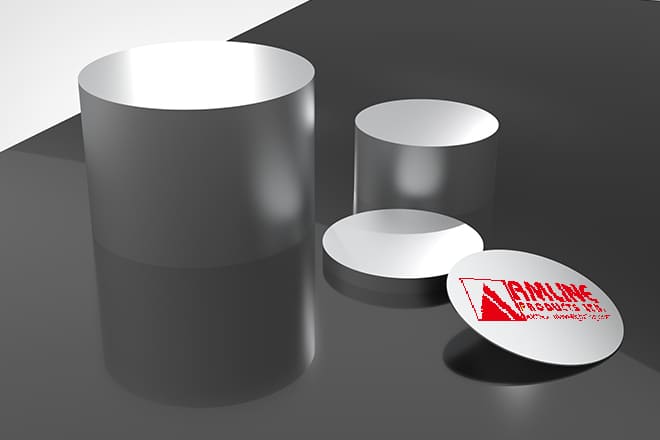
Plastic reflectors, on the other hand, offer a wide variety of material options. Most reflectors on the market are made from these two materials, PC (Polycarbonate) and ABS (Acrylonitrile Butadiene Styrene). Through careful mold polishing or surface coating, plastic reflectors can achieve effective light reflection. However, it's crucial to consider the heat resistance of the plastic used. Even within the PC material category, factors such as the polymer used, manufacturer, and thickness of the finished product can significantly impact flame resistance. When reflectors are placed near unshielded, high-voltage electrical components, selecting a material with UL 5VA flame rating ensures better safety.
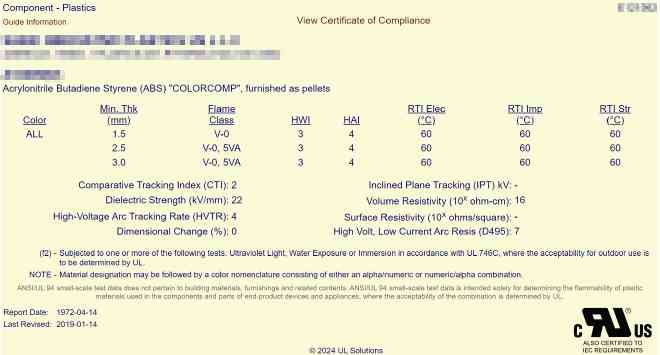
International safety standards such as UL, ETL, or CB place a strong emphasis on the flame resistance of materials used in lighting fixtures. If plastic reflectors are chosen for production, it is essential to ensure that the material meets the required specifications, as additional testing for flame resistance and weatherability is often necessary during certification. By contrast, if aluminum alloys are used for reflectors or trims, these additional tests can often be bypassed.
Still have questions about material selection? Feel free to contact Amline for more detailed consultation. We offer a variety of reflector and trim products made from aluminum or plastic(PC, PMMA, ABS … etc), and other plastic or metal materials.
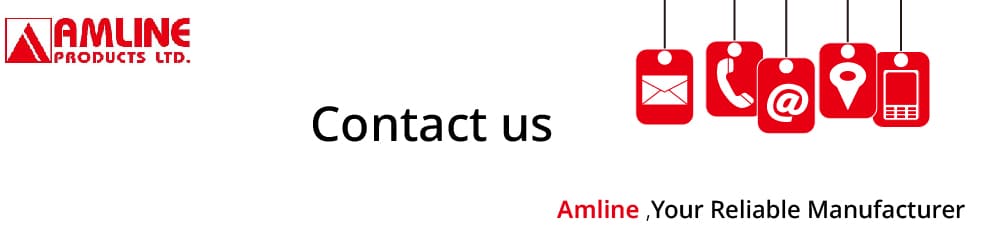